After having brewed beer for a few years, I recently went from bottling to kegging.
My reason was defeat. Too many of my batches have turned into gushers when bottled. I once discovered that one batch had become infected when I was about to bottle it, so I assumed that the other gushers had been infected, too. Although, I wasn't entirely certain, because when I managed to vent and pour a gusher, the telltale sourness of an infected beer was absent. The gushing appeared by be caused by the thin layer of sediment in the bottle being whirled up by a few bubbles, becoming a nucleous for additional CO2 bubbles and making the beer gush through the bottle neck. This would indicate over-carbonation but for this to be true, apparently the difference between almost flat and over-carbonated beer seemed to be about five to ten grams of sugar for an entire batch, and I found that unlikely.
It also seemed unlikely that boiling sugar dissolved in water for ten minutes, cooling it down, and pouring it into the beer would cause an infection. I had ruled out hygiene problems related to the bottles because I've always cleaned and disinfected the bottles thoroughly, and it was either the same kind of gushing in all 60 to 90 bottles, or nothing at all. (In case you wonder, I also paid proper attention to sterile equipment in all other steps of the bottling process.)
I finally became convinced that infection at bottling time was hardly the reason when my first lambic style beer also became a gusher. It had been sitting in its carboy for a year and a half when I primed it with sugar and new yeast then transferred it bottles. Two weeks later, they were all gushers; not violent ones, but enough to whirl the sediment into the beer and having to rush the beer into a glass. I vented and re-capped them all, and it seems I may be lucky this time. But certainly the gushing could hardly be caused by an infection considering that the beer was deliberately "infected" to begin with and everything edible had long since been digested by the bacteria.
My current hypothesis is that it was probably beer brewed with highly or moderately flocculating yeast that stayed in the bottles; low-flocculation yeast might not settle well enough on the smooth bottom of the bottles, causing just enough of it to be drawn into the beer to start the chain reaction that I'd observed earlier.
Rather than sticking (excuse the pun) to highly flocculent yeast, I figured that since kegged beer is tapped from the bottom of the keg, then even if there's sediment in the keg that provides nucleation particles for the bubbles, it will be flushed out of the keg. Hence, if my hypothesis is correct, my gushing problems should be eliminated by kegging the beer.
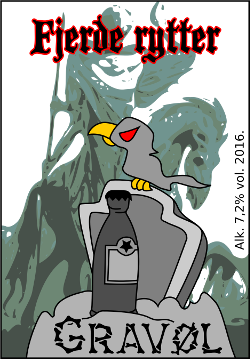
“Fjerde Rytter,” Danish for “Fourth Horseman,” is the pale rider who brings death: an appropriate name for an aggressively hopped IPA.
Maybe my hypothesis is correct, or maybe it is beginner's luck, but my first kegged beer seems to be perfect. The first two glasses tapped from the keg were a muddy mush of sediment, and I was seriously worried about my beer at first, but by the third glass the beer had cleared perfectly, and it tastes wonderful with a perfect head and not a speck of impurity in subsequent servings.
There's lots of information about force-carbonating your beer online and from what I can tell, most of the confusion and mistakes are caused by rather fundamental misunderstanding - like not realizing you should be sitting in your car seat before turning the ignition.
I nonetheless decided to purchase a complete set containing all the necessary parts: a brand new keg, hoses, a regulator, a CO2 canister, and all the necessary fittings. This way I knew I wouldn't be missing anything. Knowing what is needed for a keg, I would know what fittings to order the next time together with a used keg.
So far I've learned two minor things that I didn't see mentioned in any instructions.
Firstly, the set-and-forget force carbonation method means I identify the required pressure on a pressure chart and set the regulator accordingly; it is about as easy as it gets. The keg immediately reaches this pressure, but instead of “forgetting,” turn off the gas. Then half a day later as some the CO2 is absorbed into the beer, causing the pressure in the little room above the beer to fall, turn the gas back on for a moment to restore the pressure. This needs only being repeated about daily for the first week, then hardly at all after that. The advantage is that you won't lose CO2 if there happens to be a small leak somewhere between the CO2 inlet and the CO2 canister.
Secondly, don't attach the CO2 to the beer outlet as some suggest. Granted, the CO2 will be absorbed somewhat faster into the beer if it is allowed to bubble up through the beer, but my bet is you'll gain a few hours over an entire week at most. Meanwhile, if you don't maintain CO2 pressure, you'll risk beer pushing back into the CO2 hose and possibly into the regulator.
Both of the above approaches will reduce the carbonation speed slightly, but if you're serious about speed, probably your best bet is to avoid the set-and-forget method. I'm sufficiently patient to waiting just a few more days. Well, sort of: I couldn't help sampling, of course.
Perhaps I've learned another few things: this particular beer had been sitting in the fermentation bucket for about a month and had stopped fermenting altogether two weeks earlier. It wouldn't have hurt to let it mature a little more, however, so in the future I'll rack my beer to the kegs and have it sit there for another two weeks before applying carbonation. Also, the next beer to be kegged appears to be spiced somewhat too lightly. In contrast to bottled beer, the keg allows me to throw in a little more spice and restore the pressure.